Case Study: Utilities
Cornick and Morris delivers 90% cost saving for leading manufacturer
An industry leading manufacturer of valves used in the Gas, Water and Utilities industries approached Cornick and Morris for help with the development of a new range of Pressure Independent Control Valves. The customer wanted to use a polymer based construction, as opposed to machined brass which is traditionally used, in an effort to reduce costs.
Cornick and Morris' engineers put forward a product proposal using alternative materials and processes which they were confident would meet the overall project objectives, whilst maintaining the tight tolerances achieved through machined brass.
Using a process above the "glass transition temperature", Cornick and Morris was able to manufacture a set of valve cartridges with crystalline structure which maintained tolerances of less than 0.05mm using Polyphenylene Sulphide; the finished product range maintains all of the technical desirables of the initial design, whilst delivering a 90% cost saving over traditional materials and manufacturing processes.
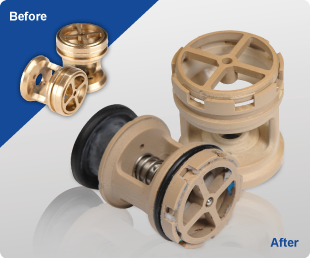
This particular project is an excellent example of the benefits of plastic injection moulding. Our experience and innovative development process meant we were able to save our customer both time and money, as well as reducing the weight of the finished product, without compromising on quality.
I am delighted that Cornick and Morris' expertise has played a direct role in giving our client a competitive edge in the market.
Steve Cornick, Managing Director
Cornick and Morris
Malvern, UK